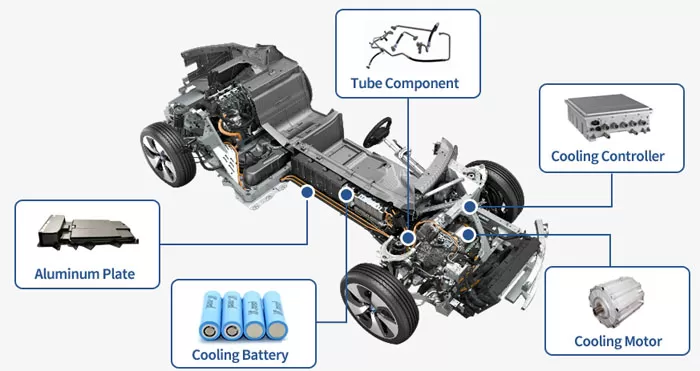
Pioneer Thermal can custom IGBT heat sink mainly application in a multi-mode vehicle thermal management system, that is provided that allows efficient thermal communication between a refrigerant-based thermal control loop (501), which may be operated in either a heating mode or a cooling mode, and multiple non-refrigerant-based thermal control loops like battery (509) control loop (505), passenger cabin control loop 503) and drive train control loop (507) . As a result of this approach, the system is able to efficiently regulate the temperature within the various vehicle thermal control loops, for example utilizing the heat generated within one subsystem (501) to heat another subsystem (503,505).
Electric vehicles driven by electricity have characteristics such as high voltage, high power, and high temperature. Power devices must adapt to the operating environment to help electric vehicles complete energy transfer and output more efficiently and energy-efficient. The thermal management of electric vehicles is an important issue, and the current thermal management solutions for electric vehicles can be roughly divided into four types: air cooling, liquid cooling, direct cooling, and phase change material cooling. Pioneer Thermal offers liquid cooling thermal management solutions according to customers' requirments. Our extensive thermal management experience with both I.C.E and electric products uniquely positions Pioneer Thermal to serve these types of vehicles.
- Electric Vehicle Thermal
Tags :